Onward Plastics’ Growth Supported by Haitian IMMs

Onward Manufacturing, a maker of gas and charcoal barbecue grills, acquired the custom molding shop making their plastic components in 1996, largely to support their own needs. In 2016, the family-owned company saw the opportunity to grow and put two family members, Andrew Sellner and Jamie Sellner, in charge of growing the custom molding side of the company.
Onward Plastics is now a fast-growing force in the Kitchener, Ontario plastics community with two operating molding facilities and 44 presses from 39 to 1750T. The company molds non-automotive highly engineered products as well as consumer products primarily made from recycled materials.
The company began replacing older machines with a new fleet of Haitian molding machines in 2019 to accommodate their growth. Onward Plastics initially purchased a two-platen JU9000 III (1,012 U.S. tons) and a servo-hydraulic MA3200 IIS (360 U.S. tons). Recently, they took delivery of its tenth Haitian, a JU1400 V (1,574 U.S. tons) equipped with extended clamp stroke, magnetic platens, tie bar puller and electric screw drive.
The energy efficiency of the JU V’s electric screw drive with parallel processing enabled Andrew Sellner, Vice President of Operations, to apply for an energy rebate from Save on Energy, the Independent ElectricitySystem Operator (IESO) supported by the Government of Ontario.
Onward Plastics processes everything from highly engineered nylons and polycarbonates to both post-consumer and post-industrial recycled materials. “We need our presses to handle everything we can throw at them, ”Andrew said. Many of our machines run recycled polypropylene and we have designed a custom screw and non-return valve specification to reduce wear and better homogenize the melt. These screws are built in North America and supplied by Absolute Haitian.
“The biggest challenge to running recycled material is the inconsistency of the material. The Haitian IMMs we are using are not doing anything special other than being rock solid and consistent.”
Onward Plastics Gains Confidence in the Absolute Haitian Relationship
Before 2019, Onward Plastics bought used machines but found that pricing for used machine, parts and service was incredibly high. “We were drawn to the fact that Haitian makes the most machines in the world and uses very standard components available from multiple sources (even though we find pricing and availability of components to be best directly from Absolute Haitian),” Andrew noted.
“Working towards a more standardized factory quickly helped our team. In 2016, we had five presses from the 1970s – a testament to the skill of our maintenance team – but that is not sustainable going forward. As we grew our number of presses, we were nearly out of power and the energy efficiency of new presses was important. Each machine is constructed in the same way. When troubleshooting, we often don’t even need to look at the drawings because the machines are so consistent and the Haitian servo-hydraulics are simple to troubleshoot.
“Absolute Haitian views parts and service in a whole different way,” Andrew said. “When we’ve needed it, Absolute Haitian has been able to get us service within a day or two. Parts are delivered overnight. We’re on a first-name basis with the guys in support and service. Everyone on the Haitian team is always happy to help us out.
One more thing Andrew appreciates. “The presses continually improve. From Mars IIS to Mars V, you can see the improvements in terms of the quality and finish of the machines. While the Generation 5 controls are different, we’re learning our way through them. The machines have met all our requirements. We continue to throw challenging projects at the machines and are happy with the outcome.”
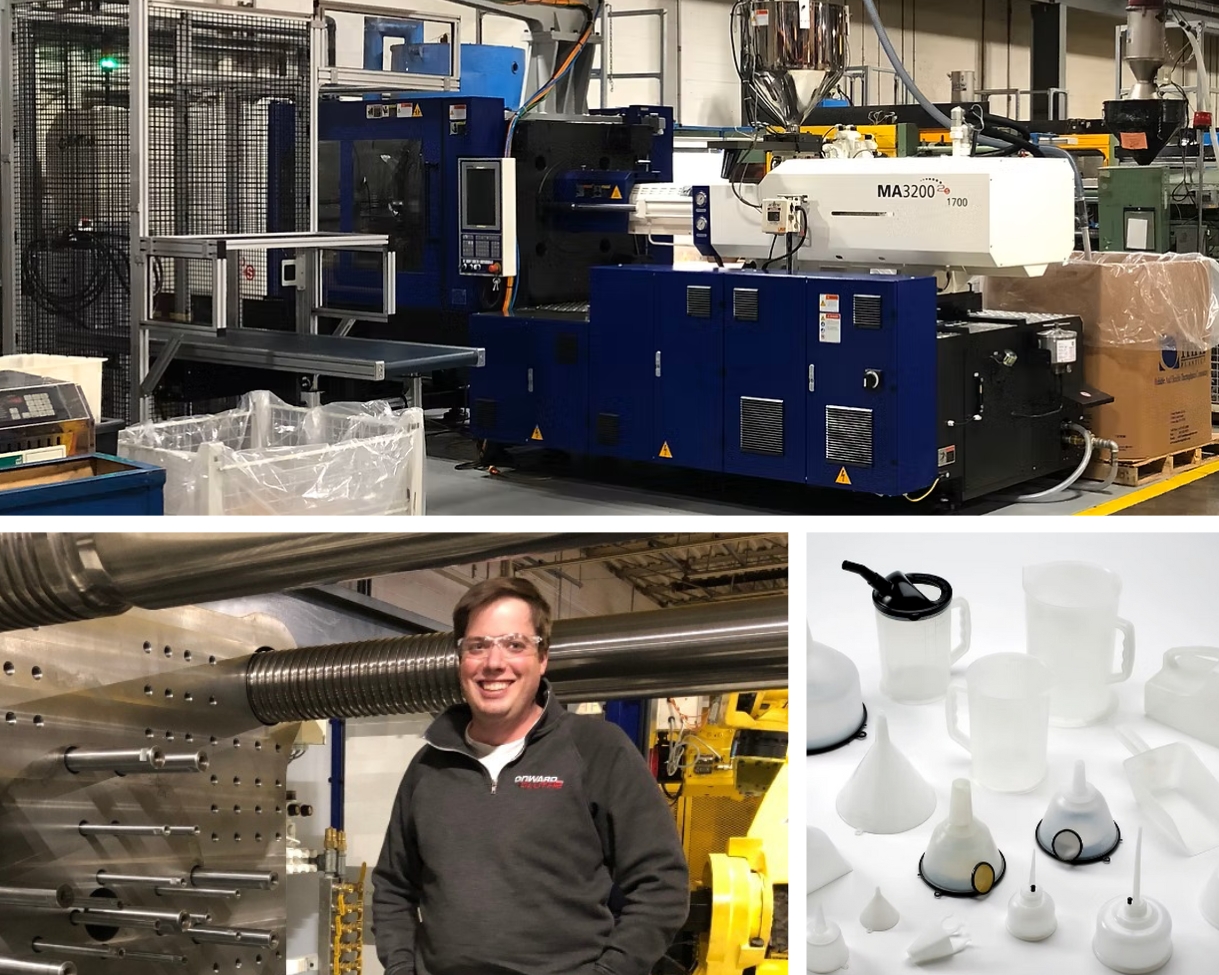